この記事はrogy Advend Calendar 2023の9日目の記事になります。
昨年度は自作した筋電計を展示させてもらいましたが、今年は自作の3Dプリンターを展示しました。
とはいえ私は電子工作やプログラミングがメインで機械の設計をしっかりとしてきたことはなく、製作中での失敗や改良したい点が多々あるものになってしまいました。
おそらく機械設計をしっかりやっている人たちにとっては当たり前な話の連続になってしまいそうですが、そんな反省点の数々を振り返っていこうと思います。
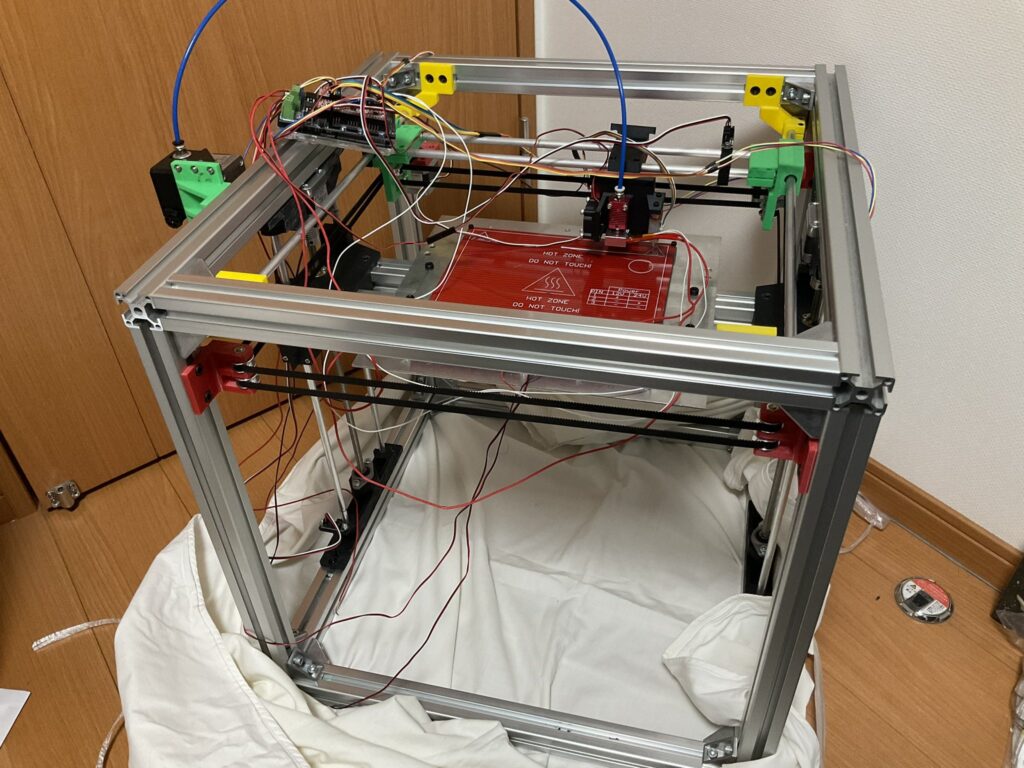
まずは3Dプリンターの構造を説明していきます。
大きさは500×500×500で制御にはArduinoMEGAとMarlinを使っています。
最近はやりのCoreXY機構を採用し、ステージが上下することでZ軸を動かします。
コンセプトとしては
- なるべく安く
- 回路、ソフト以外はなるべく自作
- 実用可能なものを作りたい
といった感じです。
それではまずこの機構を作るまでの間の反省点を振り返ってみます。
リニアブッシュをケチらない
Amazonで買った格安リニアブッシュにアルミ棒を通して使っていたのですが、当然精度がガタガタなのでリニアブッシュ一つだとグラグラします。
それだけならいいのですが、Y軸のように二つの軸が離れていると軸間でリニアブッシュがずれてまともに動きません。
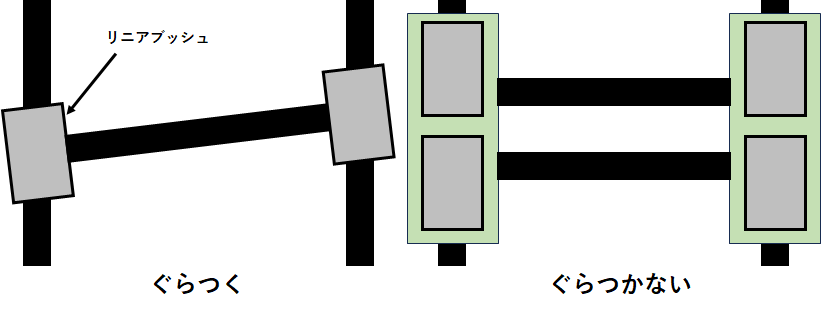
ちなみにX軸のほうではリニアブッシュをケチっています。
Y軸より2本のシャフトの距離が近いので動きはするのですが結構がたついているのでこちらも本来はケチらずリニアブッシュを4つ使ったほうが良かったですね。
動く部分は一体で作る
Z軸は2本のリニアシャフトと1本のボールねじが両側についている構造になっています。
始めて設計したときにはアルミフレームに
- 駆動用モーターを取り付ける部品
- リニアシャフトを取り付ける部品
- ボールねじを取り付ける部品
を別々に設計して取り付けようとしました。
この設計の問題はそれぞれの部品の位置を正確に合わせないといけないことです。「一番上でまず位置合わせして下まで動かして位置調整してから全部固定すればいいだろ!」と思って作ってみましたが、そんなことはなかったです。
シャフト・モーター・ボールねじの相対位置がずれるとまともに動かなくなるのでちゃんと一体部品として作りましょう。
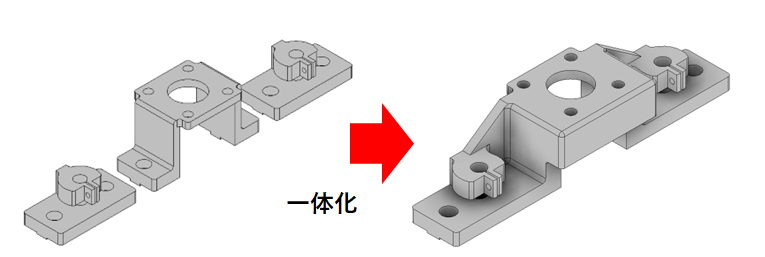
これは当然動くZ軸のステージについても同様です。最初はアルミ板に手動で穴あけしていましたが厳しくなったのでアルミフレームで作る形に切り替えました。CNCで作れるサイズを超えているのが痛かったですね。
制作にあたって起きた問題のほかに、実際に動かしてみて分かった問題点もあります。そちらも見ていきましょう。
高速で動かない
Z軸はボールねじで動いているのですが、あまりトルクの無いモータで重たいアルミフレームを2本も使ったステージを動かしていることもあるのかスピードが出ません。
そんな高性能機が作れるとは思っていなかったのでそれ自体はいいのですが、使用したスライサーが一番最初に高速でステージを下げる指令を出力していたのでステッピングモータが脱調してしまっていました。
Z軸のリミットセンサーはヒートベッドと当たらないよう印刷中は格納されるので脱調を起こして位置がずれるとそのままプリントができなくなってしまいます。
スライサー内部で速度の上限値を設定する方法などがいまいちわからなかったので結局手動でスライサーのGcodeを書き換えて対応しました。
ケーブルの配線
ステッピングモータを動かすのにモータ一つ当たり4本、ホットエンドを動かすのにヒータ電源に2本、サーミスタに2本など、あちこちに配線をしますが、適切にまとめないと絡まってトラブルの原因になります。
とくにサーミスタの配線をする際細い線が無理に曲がっていて何度か温度が検知できなくなりエラーで印刷が終了することがありました。
結局最後まで配線をまとめるのをめんどくさがってしまいましたが安全のためにも特に可動部につながっている配線はしっかりまとめるべきです。
さて、ここまでで曲がりなりにも動くものを作ることはできました。最後に実際に印刷をしてみた結果、そしてそのうえでの反省点をみていきましょう。
印刷結果
プリントしてみたのはどこかで一度は見たことがあるとは思うベンチマーク、船です。
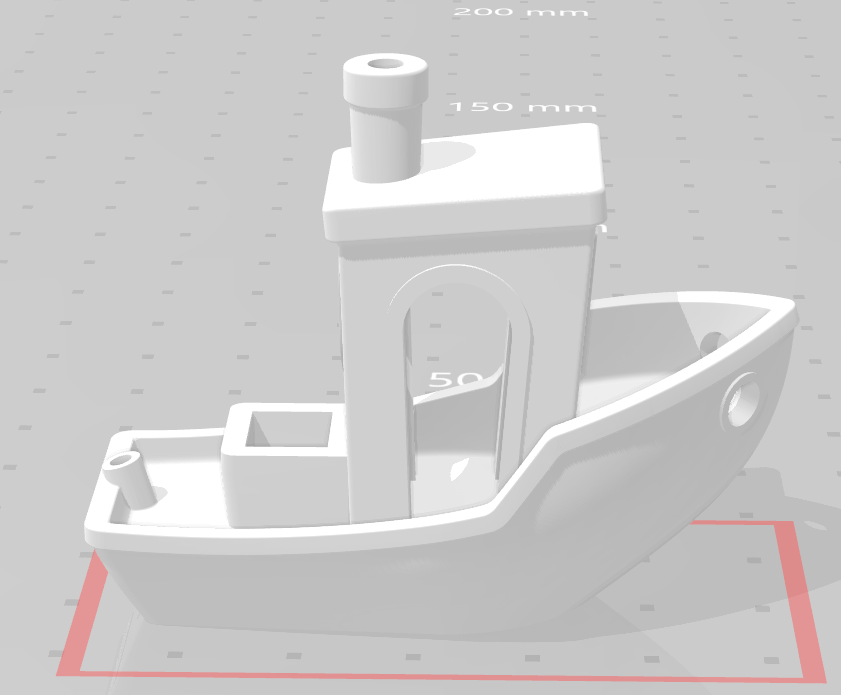
実際にこれをプリントしてみたのが以下の写真です。素材はPLA,プリント時間は1時間ほどでした。
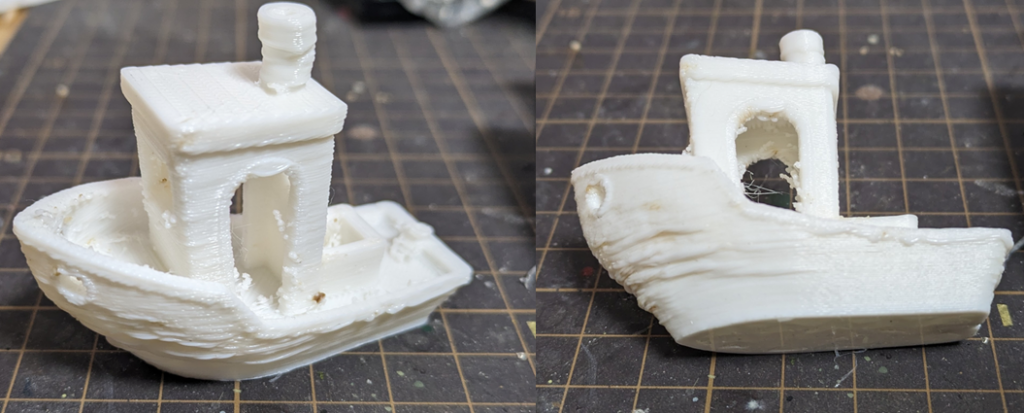
お世辞にも品質がいいとは言えませんが、もう少ししっかりと見ていきましょう。
問題点の一つ目は船の外殻の中間あたりです。層の間が凸凹しており印刷の品質が他の部分と比べても悪いですね。
他の問題は船の操舵室の入り口の部分です。まっすぐになるはずの部分からいくつも出っ張りが飛び出し糸を引いてしまっています。
これらの問題が起こった原因としては精度の不良、タイミングベルトの張力不足、冷却機構の不足を考えています。
先ほども述べたように、X軸部分でリニアブッシュをケチったせいでホットエンドがついている台座の部分の精度があまりよくありません。当然ですがホットエンドのノズルが振動すると印刷品質が低下します。
またタイミングベルトの張力が不足しているとモータの回転が伝わりにくくなります。時間がなくてタイミングベルトの張力調整機構を作れませんでした。
最後にノズルから出されたフィラメントは即座に冷却しないと糸を引くなどその場で変形してしまいます。多くの3Dプリンターではノズル付近にファンの風を当て急速に冷却する機構を取り付けていますが今回は取り付けられませんでした。
そのほか、不具合ではないのですが今回の3Dプリンターではエクストルーダ―とヘッドが分離しているボーデン式という方式を採用しました。
これはXY機構の剛性が低く、この機構の上にエクストルーダ―を載せることに不安があったからなのですが、何度かエクストルーダ―とホットエンドの間でフィラメントが詰まるトラブルがあったりしましたので可能ならダイレクト式に変えたいところです。
まとめと今後
今回はまず最後まで印刷することができる3Dプリンターを作ることができました。
現代の工作ではすっかりおなじみになった3Dプリンターですが、自分で作ってみると様々な発見があって面白かったです。
今後は
- X、Y軸の精度・剛性の改善
- 張力調整機構の追加
- ノズル先端へのファンの追加
- ソフトウェアの調整
などが課題になりそうです。
3Dプリンタもだいぶ安価になりましたが、5軸方式の3DプリンタやZ軸がベルトになっていて非常に長い物体も出力できるものなど様々なプリンタが作られています。
そういった新しいプリンタに挑戦してみたり超小型のプリンタを作ってみる、というのも面白そうです。
この記事が皆さんの参考になれば幸いです。ご覧いただきありがとうございました。